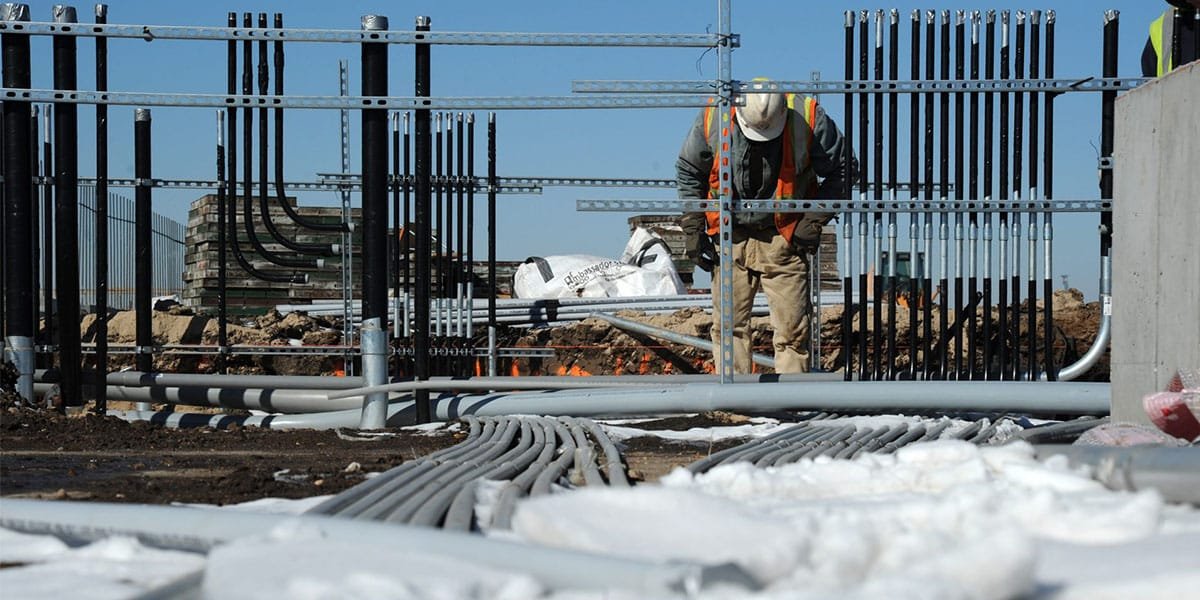
25 Mar 7 Expert Tips for Pouring Concrete in the Winter
Pouring concrete in cold weather presents unique challenges that can compromise the quality of your project. Freezing temperatures slow hydration, delaying strength gain and increasing the risk of cracks when you pour concrete. If concrete freezes too early, frost can damage the surface, and internal stresses may form, weakening the structure. Proper preparation and temperature control are essential when you pour concrete. For example, maintaining a consistent curing temperature below a 35 °F gradient prevents thermal cracking. By managing these factors, you can ensure your concrete cures properly and achieves lasting durability.
Preparing the Site for Cold Weather Concrete Pouring
Clearing Snow, Ice, and Debris
Before you pour concrete in winter, clearing the site is essential. Snow, ice, and debris can compromise the foundation and create safety hazards. Start by removing all snow and ice from the work area. Use shovels or non-corrosive de-icing agents to ensure the surface is clean and slip-free. Salting the area can also help prevent ice from forming again. A clean site ensures proper bonding between the concrete and the ground, which is critical for durability.
Tip: Always check for hidden ice patches that could cause accidents or weaken the foundation.
Insulating the Ground Before Pouring
Cold weather can freeze the ground, making it unsuitable for concrete pouring. Insulating the ground helps maintain the minimum temperatures needed for proper curing. Use insulated blankets or plastic sheets to trap heat and keep moisture out. Pre-warming the site with tarps or heaters can also stabilize the temperature. Insulated concrete forms are another effective option, as they retain heat within the wall assembly. These methods ensure the ground stays warm enough to support the curing process.
Note: Thawing frozen ground before pouring prevents uneven curing and structural issues.
Choosing the Right Tools for Winter Conditions
Using the right tools can make pouring concrete in winter more efficient. Hydronic heaters and electric space heaters provide consistent heat to the site. Insulated forms trap warmth, ensuring the concrete cures evenly. For real-time monitoring, consider using SmartRock technology. This wireless sensor tracks temperature and strength, allowing you to make precise adjustments. These tools help you maintain control over the curing process, even in cold weather.
Pro Tip: Investing in tools designed for winter conditions reduces delays and improves the quality of your project.
Adjusting the Concrete Mix for Cold Weather
Using Cold Weather Additives
Cold weather additives can significantly improve the performance of concrete during winter. These additives accelerate the curing process and help maintain strength even in low temperatures. For example, calcium chloride is a common accelerator that speeds up hydration and generates heat. However, it may increase the risk of corrosion in steel reinforcements. Non-chloride accelerators provide a safer alternative, especially for projects requiring reinforced concrete.
Air-entrained concrete is another effective solution for cold climates. It contains tiny air pockets that resist freeze-thaw cycles, reducing the risk of cracks and scaling. This feature enhances the durability of your project, especially in areas with fluctuating temperatures.
Tip: Always check your project specifications before using additives. Some guidelines restrict the use of chlorides or other materials in concrete mixes.
Benefits | Limitations |
---|---|
Higher-strength mixes lead to early strength gain | Calcium chloride can increase corrosion risk in reinforcing steel, leading to premature deterioration. |
Allows faster formwork removal | Mineral admixtures may retard initial strength gain, especially in cold weather. |
Use of non-chloride accelerators is safer | Specifications often limit or restrict the use of chlorides in concrete. |
Air-entrained concrete minimizes freeze-thaw damage | Caution is advised when using mineral admixtures during cold weather periods. |
Opting for Low-Temperature Concrete Mixes
Choosing the right mix design is crucial when you pour concrete in cold weather. A lower water-to-cement ratio reduces the risk of freezing and improves overall strength. Using a drier mix with less water is a practical way to achieve this. To maintain workability, you can add flow-enhancing admixtures. Warm water is another option to raise the temperature of the mix, ensuring proper hydration during curing.
For faster strength gain, consider using Type III cement. This type of cement generates heat more quickly, which helps the concrete set faster in cold conditions. Increasing the amount of Portland cement in the mix can also enhance early strength. However, reducing fly ash or ground slag content is advisable, as these materials may slow down the curing process in low temperatures.
Air-entrained concrete is another excellent choice for winter projects. Its air bubbles act as buffers, preventing damage from freeze-thaw cycles. This feature ensures your concrete remains durable even in harsh weather conditions.
Note: Always monitor the minimum temperatures required for curing to avoid freezing during the process.
Monitoring Temperatures During Pouring and Curing
Checking Weather Forecasts and Planning Ahead
Monitoring the weather is essential when you pour concrete in cold weather. Sudden temperature changes can disrupt the curing process and weaken the final structure. Before starting your project, check the forecast for freezing temperatures, snow, or rain. This helps you plan the best time to pour and ensures the curing process remains uninterrupted.
If the forecast predicts extreme cold, consider delaying the project or preparing additional measures like heaters or insulating blankets. These tools help maintain the minimum temperatures required for proper curing. Planning ahead reduces risks and ensures your concrete achieves the desired strength and durability.
Tip: Always have a backup plan for unexpected weather changes to avoid costly delays.
Using Thermometers to Track Concrete Temperatures
Tracking concrete temperatures during curing is crucial for success in cold weather. Use thermometers or temperature sensors to monitor the internal heat of the concrete. Tools like the AKCP wireless temperature sensor provide real-time data and allow remote monitoring. This eliminates guesswork and ensures accurate control over curing conditions.
For more advanced monitoring, consider temperature recorders or data loggers. Models with remote thermocouple probes or submersible loggers offer convenience and precision. These tools help you maintain consistent curing temperatures, even in challenging conditions.
Maintaining proper heat levels prevents freezing and ensures the concrete sets correctly. By using these tools, you can confidently manage the curing process and achieve long-lasting results.
Pro Tip: Regularly check the temperature during curing to avoid issues caused by sudden drops in heat.
Protecting Concrete During the Curing Process

Using Insulating Blankets and Covers
To protect concrete in cold weather, insulating blankets and covers are essential tools. These materials help retain heat and prevent freezing during the curing process. Concrete curing blankets, made from tough woven polyethylene fabric, offer exceptional durability and waterproofing. They resist UV rays, tears, and mildew, making them ideal for outdoor use. Lightweight and easy to handle, these blankets are effective even in temperatures below 20°F.
For added efficiency, select blankets with high R-values, which measure insulation performance. Options with R-values up to 7.7 provide excellent thermal protection. Some blankets also feature grommets for secure placement and are available in various sizes to suit your project needs. Wet concrete curing blankets are another option, as they prevent moisture loss in warmer conditions while maintaining proper curing in cold weather.
Feature | Description |
---|---|
Material | Tough woven polyethylene fabric for superior insulation and durability. |
Insulation Thickness | Range of insulating foam thicknesses providing excellent protection and high R-values. |
R-Value | Available R-values up to 7.7 for effective insulation. |
Durability | Resilient, hydrophobic micro-foam with a tough poly outer shell. |
Special Features | Grommets for securing, available in various sizes, and options for wet weather conditions. |
Maintaining Consistent Heat Levels
Maintaining consistent heat levels is crucial for proper curing when you pour concrete in cold weather. Several methods can help you achieve this. Live steam, maintained at around 140°F, ensures the concrete reaches the desired strength. Heating coils placed near the surface prevent freezing and maintain optimal curing temperatures.
Electrical heated forms or pads are another effective solution, commonly used by precast concrete suppliers. For smaller projects, concrete blankets with built-in heating systems offer a convenient way to regulate temperatures. These methods ensure the curing process remains uninterrupted, even in freezing conditions.
Tip: Monitor the temperature regularly to avoid sudden drops that could compromise the curing process.
Preventing Freezing While Pouring Concrete
Avoiding Frozen Ground and Thawing the Site
Pouring concrete on frozen ground can lead to several issues, including cracked surfaces, delayed curing, and structural instability. Frozen ground prevents proper bonding between the concrete and the base, which compromises the durability of your project. To avoid these risks, you must prepare the site thoroughly.
- Clear Snow and Ice: Remove all snow and ice from the area before starting. Use shovels or non-corrosive de-icing agents to ensure the surface is clean and safe.
- Thaw the Ground: Use ground heaters to warm the site and prevent freezing. These heaters stabilize the temperature, creating a suitable environment for curing.
- Insulate the Ground: Cover the area with insulated blankets or plastic sheets to retain heat and protect the ground from frost.
Additionally, using warm water in your concrete mix can improve hydration rates, ensuring the material sets properly. These steps help you prevent freezing and maintain the integrity of your project.
Tip: Always inspect the ground for hidden frost patches that could weaken the foundation.
Preparing for Sudden Temperature Drops
Sudden temperature drops can disrupt the curing process and damage freshly poured concrete. To protect concrete in cold weather, you need to anticipate and prepare for these changes.
- Monitor Weather Conditions: Regularly check forecasts to identify potential cold fronts or snowstorms.
- Extend Curing Time: Be ready to maintain insulation and heating measures for longer periods if temperatures drop unexpectedly.
- Use Insulated Blankets: Cover the concrete immediately after pouring to retain heat and prevent freezing.
- Set Up Windbreaks: Install barriers around the site to shield the concrete from cold winds that can lower its temperature.
- Create a Heated Enclosure: For larger projects, consider building a temporary heated enclosure to maintain consistent curing conditions.
By staying proactive, you can prevent freezing and ensure your concrete achieves the desired strength and durability.
Pro Tip: Schedule your pour during the warmest part of the day to minimize exposure to freezing temperatures.
Ensuring Safety During Cold Weather Concrete Pouring
Wearing Proper Winter Gear
Working in cold weather requires the right clothing to keep you safe and comfortable. You should wear at least three layers of loose-fitting clothing. The inner layer should wick moisture away from your skin, the middle layer should provide insulation, and the outer layer should protect against wind and rain. Insulated waterproof gloves and boots are essential to keep your hands and feet warm and dry.
Tip: Use hand warmers inside your gloves for extra warmth during long shifts.
Additional protective gear, such as parkas, bombers, and hard liners, can shield you from extreme cold. Always recognize the early signs of cold stress, such as shivering or numbness, and take breaks in a warm area when needed. Following OSHA’s cold stress guidelines ensures a safer working environment for everyone on-site.
Handling Additives and Equipment Safely
Handling additives and equipment in cold weather requires extra caution. Many cold-weather additives, like calcium chloride, can irritate your skin. Always wear gloves and safety goggles when mixing or applying these materials. If you’re using non-chloride accelerators, follow the manufacturer’s instructions to avoid improper mixing, which could affect the concrete’s strength.
When operating heaters or other equipment, inspect them for damage before use. Faulty equipment can pose fire hazards or release harmful fumes. Keep heaters at a safe distance from flammable materials and ensure proper ventilation to prevent carbon monoxide buildup.
Pro Tip: Regularly check your tools and equipment for ice buildup, which can cause malfunctions or accidents.
By prioritizing safety, you can focus on achieving proper curing and completing your project without unnecessary risks.
Post-Curing Maintenance for Winter Concrete Projects
Inspecting for Cracks and Damage
After curing, inspecting your concrete for cracks and damage ensures its long-term durability. Winter conditions often cause specific types of damage that you can identify with a careful visual inspection:
- Scaling: Look for thin layers of the surface peeling away, which often appears as small scales or flakes.
- Spalling: Check for deeper damage, especially at joints or edges, where coarse aggregate may become exposed. This type of damage can range from 1/8 inch to several inches in depth.
- Cracking: Examine the surface for unplanned cracks caused by contraction during cold temperatures. These cracks can weaken the structure if left untreated.
Addressing these issues early prevents further deterioration. For minor cracks, use a concrete patching compound. For more severe damage, consult a professional to assess the structural integrity. Regular inspections are one of the most effective curing tips to maintain the quality of your project.
Tip: Perform inspections during daylight hours to spot subtle signs of damage more easily.
Applying Sealants for Freeze-Thaw Protection
Sealants play a critical role in protecting concrete from freeze-thaw cycles. Water that seeps into the concrete can freeze, expand, and cause cracks. Applying a high-quality penetrating sealer creates a barrier against water absorption, reducing the risk of freeze-thaw damage.
Consider using Siloxa-Tek 8500, a sealant that combines silane and siloxane. This product forms a hydrophobic barrier, preventing excessive moisture from entering the concrete. It’s especially effective in areas with frequent freeze-thaw cycles.
To apply a sealant:
- Clean the surface thoroughly to remove dirt, oil, or debris.
- Use a roller or sprayer to apply the sealant evenly.
- Allow the sealant to cure according to the manufacturer’s instructions.
Pro Tip: Reapply sealants every few years to maintain their effectiveness and extend the life of your concrete.
By inspecting for damage and applying sealants, you can protect your concrete from harsh winter conditions and ensure its durability for years to come.
Pouring concrete in winter requires careful planning and execution to overcome the challenges posed by freezing temperatures. By following these seven expert tips, you can achieve durable and long-lasting results:
- Select the right concrete mix, such as air-entrained concrete, to resist freeze-thaw cycles.
- Pre-heat materials like water and aggregates to prevent freezing.
- Protect freshly poured concrete with heated enclosures and insulating blankets.
- Monitor temperatures consistently to maintain the ideal temperature to pour concrete.
- Thaw frozen ground and insulate the site to ensure proper curing.
- Wear appropriate winter gear and handle additives safely to avoid accidents.
- Inspect cured concrete for cracks and apply sealants for freeze-thaw protection.
To ensure success, use modern tools like thermal enclosures and insulated blankets, and follow professional guidelines like ACI Committee 306. These strategies help maintain curing conditions and enhance the strength of your project. Always prioritize safety and consult professionals for complex tasks. With the right approach, you can confidently tackle any cold-weather concrete project.