
25 Jan A Guide to Different Types of Concrete Testing
Concrete testing plays a vital role in ensuring the safety and durability of construction projects. By conducting quality tests, you can verify the material’s strength and identify potential issues before they escalate. Every concrete structure demands strict testing procedures to meet safety standards and maintain long-term performance. Poor-quality testing increases the risk of rejecting good concrete, leading to delays and higher costs. Selecting the right types of concrete tests ensures accurate results, helping you avoid structural failures and enhance project efficiency. Testing is not just a step; it’s a safeguard for your construction’s integrity.
Tests for Fresh Concrete
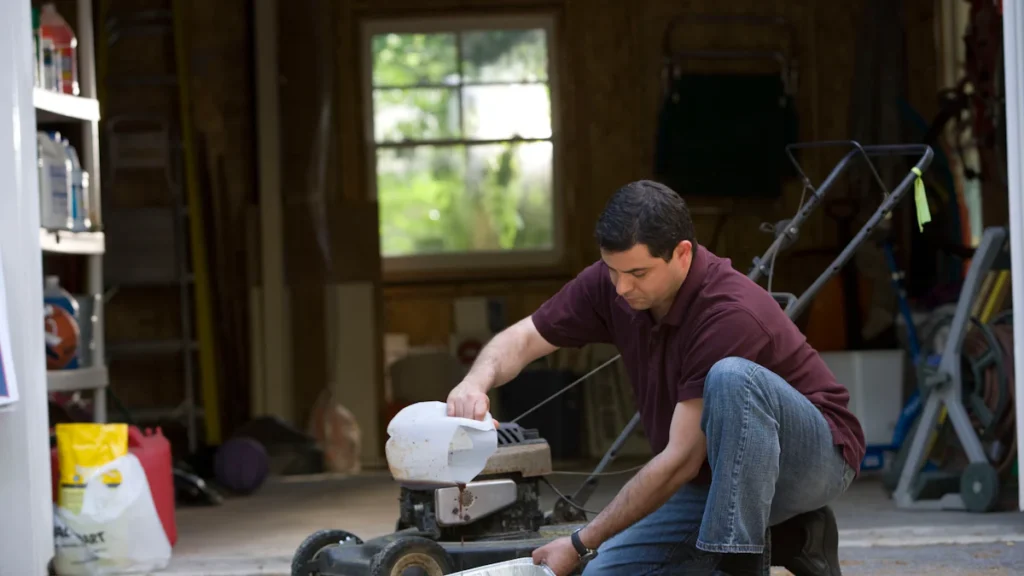
Testing fresh concrete ensures its quality and suitability for construction. These tests help you evaluate the workability, consistency, and other essential properties of the material before it hardens. Below are some of the most common fresh concrete tests.
Slump Test
The slump test is one of the simplest and most widely used methods to assess the workability of fresh concrete. It measures how much the concrete subsides or “slumps” when a cone-shaped mold is lifted. This test helps you determine if the concrete mix has the right consistency for your project.
To perform the test, you need a slump cone, a tamping rod, and a base plate. Fill the cone with concrete in three layers, tamping each layer 25 times with the rod. Once the cone is full, lift it vertically and measure the height difference between the top of the cone and the slumped concrete. A higher slump indicates a more workable mix, while a lower slump suggests a stiffer mix. Tools like the Bon Tool 82-485 Slump Test Kit provide all the necessary components for accurate results.
Air Content Test
The air content test measures the amount of air trapped in fresh concrete. Proper air content improves durability, especially in freeze-thaw conditions. This test is crucial for ensuring the concrete can withstand environmental stresses without cracking.
You can use devices like the Type B pressure meter or volumetric method equipment for this test. The pressure method involves applying pressure to a sample of concrete to determine its air content. Accurate tools, such as Forney Press-Aire Meters, ensure reliable measurements. Maintaining the correct air content enhances the concrete’s performance and longevity.
Temperature Test
Temperature plays a critical role in the setting and strength development of concrete. Monitoring the temperature of fresh concrete ensures it meets the required specifications for proper curing and hardening. Extreme temperatures can lead to issues like cracking or delayed strength gain.
To conduct this test, use a thermometer or temperature probe to measure the concrete’s temperature immediately after mixing. This simple yet essential step helps you avoid potential problems caused by improper curing conditions.
Unit Weight Test
The unit weight test determines the density of fresh concrete, which is essential for assessing its quality and consistency. This test helps you calculate the weight of concrete per unit volume, ensuring that the mix meets the required specifications for your project. By performing this test, you can also estimate other critical properties, such as yield, cement content, and air content.
To conduct the unit weight test, you need a container of known volume, a scale, and fresh concrete. Follow these steps:
- Weigh the empty container to record its weight.
- Fill the container with fresh concrete in three layers, tamping each layer 25 times to eliminate air voids.
- Weigh the filled container and subtract the weight of the empty container to find the net weight of the concrete.
- Divide the net weight by the container’s volume to calculate the unit weight.
For example, if the net weight of the concrete is 50 pounds and the container’s volume is 0.5 cubic feet, the unit weight would be 100 pounds per cubic foot.
This test provides valuable insights into the mix’s uniformity and helps you identify potential issues, such as excessive air content or improper proportions. Consistent unit weight results indicate a well-mixed concrete batch, while significant variations may signal problems that require immediate attention.
Accurate unit weight measurements contribute to the success of your construction project. They ensure that the fresh concrete tests align with design requirements, enhancing the structure’s durability and performance.
Tests for Hardened Concrete
Hardened concrete tests evaluate the strength and durability of concrete after it has set and cured. These tests ensure that the material meets the structural requirements of your project. Below are three critical tests used to assess hardened concrete.
Compressive Strength Test
The compressive strength test is one of the most important methods in concrete strength testing. It measures the ability of concrete to withstand axial loads without failing. This test helps you determine if the concrete meets the required strength for your project.
To perform this test, you need cylindrical or cubical concrete specimens. These specimens are cured for specific durations, typically 3, 7, and 28 days. After curing, you place the specimen in a compression testing machine and apply force until it breaks. The maximum load the specimen can bear before failure is recorded as its compressive strength.
For example, if a concrete cylinder withstands a load of 100,000 pounds and has a cross-sectional area of 50 square inches, its compressive strength would be 2,000 psi.
Compressive strength testing is essential for ensuring the quality and sturdiness of concrete. It also provides insights into the mix design, water-cement ratio, and curing conditions. Consistent results indicate that the concrete is durable and capable of supporting heavy loads.
Tensile Strength Test
Concrete is inherently weak in tension, making tensile strength tests crucial for identifying the load at which cracks may develop. These tests help you understand how the material will perform under tensile forces, such as those caused by temperature changes or structural movements.
One common method for conducting a tensile strength test is the split-cylinder test. In this method, you place a cylindrical concrete specimen horizontally in a testing machine. The machine applies a compressive load along the length of the cylinder, creating tensile stress perpendicular to the applied force. The load at which the specimen splits is recorded as its tensile strength.
Another method involves direct tension testing, where a concrete specimen is pulled apart until it fails. Although less common, this method provides accurate results for tensile strength.
Tensile strength tests are vital for preventing structural failures caused by cracking. They also help you design reinforcements, such as steel bars, to compensate for concrete’s low tensile strength.
Flexural Strength Test
The flexural strength test evaluates the ability of concrete to resist bending or flexural forces. This test is particularly important for structures like beams, slabs, and pavements, where bending stresses are common.
To conduct this test, you use a rectangular concrete beam specimen. The specimen is supported at both ends and subjected to a load at the center or at two points equidistant from the supports. The load is gradually increased until the specimen fails. The maximum stress experienced by the specimen before failure is recorded as its flexural strength.
Flexural strength tests provide valuable information about the tensile properties of concrete. They also help you assess the quality of the mix and its suitability for specific applications. A higher flexural strength indicates better resistance to cracking and deformation under bending forces.
By performing these hardened concrete tests, you can ensure that your structure meets safety standards and performs well under various loads. These tests also help you identify potential issues early, reducing the risk of costly repairs or failures.
Permeability Test
The permeability test evaluates how well concrete resists the penetration of liquids and gases. This property directly impacts the durability of your structure. High permeability can lead to issues like water absorption, corrosion of steel reinforcements, and reduced lifespan of the concrete. By conducting this test, you can ensure that the concrete mix meets the necessary standards for long-term performance.
One common method involves applying water pressure to cured concrete samples using specialized equipment. The depth of water penetration is then measured to determine the permeability level. For accurate results, you can use tools like Permeability Test Equipment, which are designed to handle this process efficiently. Lower permeability indicates better resistance to environmental factors, enhancing the durability of your construction.
Understanding permeability helps you identify potential weaknesses in the concrete. It also allows you to adjust the mix design, such as optimizing the water-cement ratio, to improve the material’s resistance to moisture and other external elements.
Drilled Core Test
The drilled core test is a reliable method for assessing the strength and quality of hardened concrete. This test involves extracting cylindrical cores from the structure and analyzing them in a laboratory. It provides valuable insights into the actual performance of the concrete in its final state.
To perform this test, you use a core drilling machine to remove a sample from the hardened concrete. The extracted core undergoes compressive strength testing to measure its ability to withstand axial loads. This process helps you verify if the concrete meets the required strength specifications for your project. For example, if the core fails under a specific load, it may indicate issues with the mix design or curing process.
The drilled core test is particularly useful for evaluating older structures or verifying the quality of newly constructed elements. It ensures that the concrete aligns with safety standards and performs as expected under various conditions.
Cast-in-place Cylinders
The cast-in-place cylinder test evaluates the strength of concrete in its actual position within the structure. Unlike other methods, this test involves casting cylinders directly at the construction site during the pouring process. These cylinders are then cured and tested to determine their compressive strength.
To conduct this test, you place molds at the site and fill them with fresh concrete from the same batch used for the structure. After curing, the cylinders undergo compressive strength tests to measure their load-bearing capacity. This method provides an accurate representation of the concrete’s performance in real-world conditions.
Using tools like Cast-in-place Cylinder Molds ensures consistency and precision during the testing process. The results help you confirm that the concrete meets the design requirements and performs well under expected loads. This test is essential for maintaining the integrity and safety of your construction project.
Specialized Concrete Tests
Specialized concrete tests provide deeper insights into the properties and performance of concrete. These methods often focus on specific characteristics, helping you evaluate the material’s quality and suitability for unique applications. Below are three widely used specialized tests.
Rebound Hammer Test
The rebound hammer test offers a quick and cost-effective way to assess the surface hardness of concrete. This method uses a spring-loaded hammer to strike the concrete surface, measuring the rebound distance to estimate compressive strength. You can use this test to check the uniformity of concrete across different sections of a structure.
To perform the test, hold the rebound hammer perpendicular to the concrete surface and release the hammer. The rebound value, displayed on the device, correlates with the concrete’s compressive strength. This method is non-destructive, making it ideal for evaluating existing structures without causing damage. According to a study published in the European Journal of Engineering and Technology Research, the rebound hammer provides a faster and more economical way to ensure concrete uniformity.
This test is particularly useful for preliminary assessments or when you need to identify weak spots in a structure. However, it works best when combined with other methods, as surface hardness alone may not fully represent the concrete’s overall strength.
Ultrasonic Pulse Velocity Test
The ultrasonic pulse velocity test measures the speed of ultrasonic waves traveling through concrete. This method helps you evaluate the material’s quality, detect voids, and estimate its compressive strength. It is a non-destructive technique that provides valuable insights into the integrity of concrete structures.
To conduct this test, place a transmitter and receiver on opposite sides of the concrete. The transmitter sends ultrasonic pulses, and the receiver measures the time it takes for the waves to pass through the material. Faster wave speeds indicate denser and higher-quality concrete. The SONREB method, which combines ultrasonic pulse velocity with rebound hammer results, allows for more accurate correlations to compressive strength.
This test is ideal for assessing large structures like bridges or dams, where traditional methods may be impractical. It also helps you monitor the condition of aging structures, ensuring their safety and durability over time.
Pullout Test
The pullout test evaluates the bond strength of concrete by measuring the force required to extract a metal insert embedded in the material. This method provides direct insights into the concrete’s strength and its ability to hold reinforcements securely.
To perform the test, embed a metal insert into the fresh concrete during casting. Once the concrete hardens, attach a pulling device to the insert and apply force until it is extracted. The maximum force recorded indicates the bond strength. This test is particularly useful for assessing the quality of concrete in critical areas, such as columns or beams.
The pullout test offers reliable results and helps you identify potential weaknesses in the concrete. It is especially valuable for ensuring that the material meets the required specifications for load-bearing elements in your project.
Drying Shrinkage Test
The drying shrinkage test evaluates how much concrete contracts as it loses moisture over time. This contraction can lead to cracks, reducing the durability and lifespan of your structure. Understanding this property helps you design concrete mixes that minimize shrinkage and maintain structural integrity.
To perform the test, you cast concrete specimens in molds and cure them under controlled conditions. After curing, you measure the initial length of the specimens. Then, you expose them to a drying environment and periodically measure their length over time. The difference between the initial and final lengths indicates the amount of shrinkage.
For example, if a concrete specimen initially measures 300 mm and shrinks by 1.5 mm after drying, the shrinkage strain would be 0.005%.
Shrinkage can vary depending on factors like the water-cement ratio, aggregate type, and environmental conditions. Adding materials such as polypropylene fibers can reduce shrinkage and improve the concrete’s performance. A study published in Construction and Building Materials found that incorporating 2% polypropylene fibers significantly enhanced the residual mechanical properties of concrete during heating, which can also mitigate shrinkage-related issues.
By conducting the drying shrinkage test, you can identify potential problems early and adjust the mix design to prevent cracking. This ensures your structure remains durable and resistant to environmental stresses.
Chloride Ion Penetration Test
The chloride ion penetration test measures the ability of concrete to resist chloride ions, which can cause corrosion in steel reinforcements. Corrosion weakens the structure and reduces its lifespan. This test is essential for projects exposed to marine environments or deicing salts.
To conduct the test, you prepare concrete specimens and subject them to an electrical charge. The charge drives chloride ions into the concrete, and you measure the amount of current passed over a specific period. Lower current values indicate better resistance to chloride penetration.
For instance, concrete with a low water-cement ratio typically shows higher resistance to chloride ions due to its dense microstructure.
Improving the concrete’s resistance to chloride ions involves optimizing the mix design. Reducing the water-cement ratio and using supplementary cementitious materials like fly ash or silica fume can enhance durability. This test helps you ensure that your concrete meets the required standards for long-term performance in harsh environments.
Alkali-Silica Reaction (ASR) Test
The alkali-silica reaction (ASR) test identifies the potential for harmful chemical reactions between alkalis in cement and reactive silica in aggregates. This reaction produces a gel that absorbs moisture, causing the concrete to expand and crack. ASR can compromise the structural integrity of your project.
To perform the test, you immerse concrete specimens containing reactive aggregates in a high-alkaline solution. Over time, you monitor the specimens for signs of expansion. The degree of expansion indicates the likelihood of ASR occurring in the concrete.
For example, if a specimen expands by more than 0.1% within 14 days, it may indicate a high risk of ASR.
Preventing ASR involves selecting non-reactive aggregates and using low-alkali cement. Adding supplementary materials like fly ash can also mitigate the reaction. By conducting the ASR test, you can ensure that your concrete remains stable and free from expansion-related damage.
Non-Destructive Testing Methods
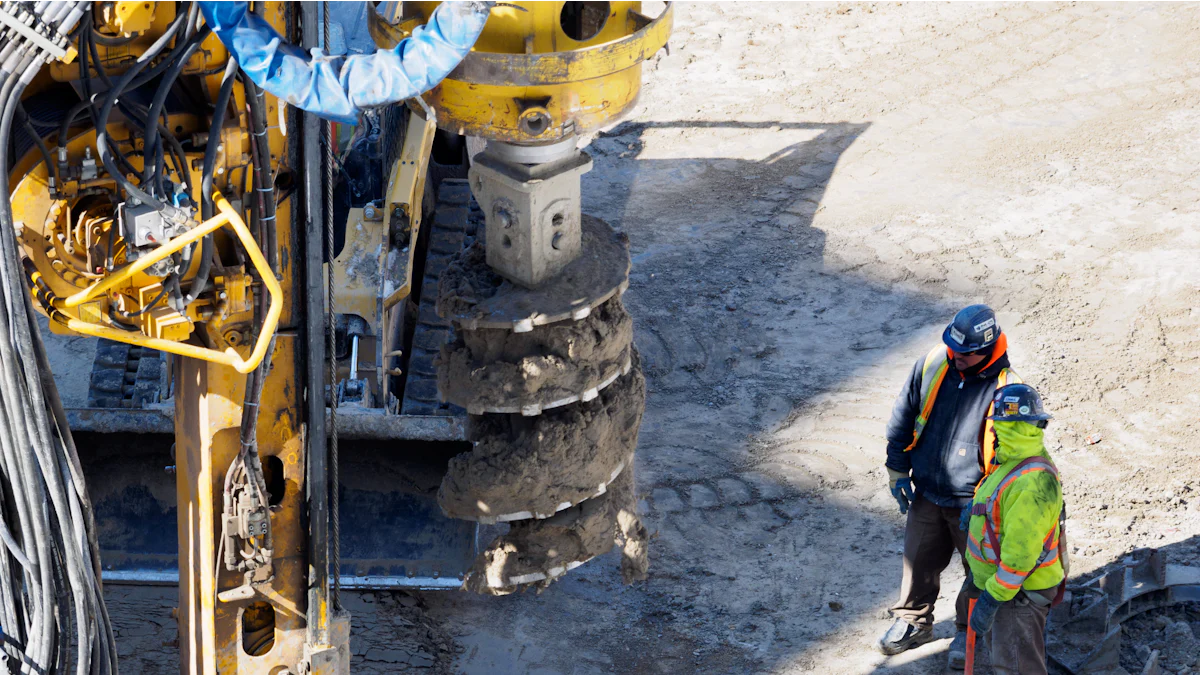
Non-destructive testing (NDT) methods allow you to evaluate concrete without causing damage to the structure. These techniques are ideal for assessing the quality and integrity of both new and existing concrete. Below are three widely used NDT methods that provide valuable insights into the material’s performance.
Rebound Hammer Test
The rebound hammer test offers a quick and straightforward way to assess the surface hardness of concrete. This method uses a spring-loaded hammer to strike the concrete surface, measuring the rebound distance to estimate its compressive strength. You can use this test to identify variations in surface quality across different areas of a structure.
To perform the test, hold the rebound hammer perpendicular to the concrete surface and release the hammer. The rebound value displayed on the device correlates with the concrete’s compressive strength. This method works particularly well for aging concrete, where surface hardness can indicate wear or deterioration. However, it only evaluates the surface layer, so combining it with other methods provides a more comprehensive assessment.
For example, if the rebound value is consistently low in certain areas, it may indicate weaker concrete that requires further investigation.
The rebound hammer test is cost-effective and easy to use, making it a popular choice for preliminary assessments. It helps you quickly identify potential weak spots without disrupting the structure.
Ultrasonic Pulse Velocity Test
The ultrasonic pulse velocity (UPV) test measures the speed of ultrasonic waves traveling through concrete. This method helps you detect internal defects, such as voids or cracks, and assess the material’s density. Unlike the rebound hammer test, UPV evaluates the entire cross-section of the concrete, providing a more detailed analysis.
To conduct this test, place a transmitter and receiver on opposite sides of the concrete. The transmitter sends ultrasonic pulses, and the receiver measures the time it takes for the waves to pass through the material. Faster wave speeds indicate denser and higher-quality concrete. This method works well for new concrete and large structures like bridges or dams, where internal integrity is critical.
For instance, if the wave speed is significantly slower in one section, it may suggest the presence of voids or poor-quality concrete.
The UPV test is non-invasive and highly effective for monitoring the condition of concrete over time. It ensures that your structure remains safe and durable, even under challenging conditions.
Penetration Resistance Test
The penetration resistance test evaluates the surface strength of concrete by measuring the force required to drive a pin or probe into the material. This method provides insights into the surface hardness and helps you identify areas that may need repair or reinforcement.
To perform the test, use a specialized device to drive a pin into the concrete surface. The depth of penetration correlates with the material’s strength. While this method is less accurate than others, it offers a simple way to assess surface quality. It works best when used alongside more comprehensive tests like UPV or rebound hammer.
For example, if the penetration depth is unusually high in certain areas, it may indicate surface deterioration or low-strength concrete.
The penetration resistance test is practical for quick evaluations, especially in smaller projects or areas with visible damage. It helps you make informed decisions about maintenance and repairs.
By using these non-destructive testing methods, you can assess the quality and safety of concrete without compromising its integrity. Each method has unique strengths, so combining them often yields the most reliable results.
Wireless Maturity Sensors
Wireless maturity sensors have revolutionized the way you monitor concrete curing and strength development. These advanced devices provide real-time data, allowing you to make informed decisions without relying on traditional methods that often require third-party labs or time-consuming processes.
To use wireless maturity sensors, you embed them within the concrete formwork during the pouring process. These sensors track temperature and time, two critical factors in determining concrete strength. By applying the maturity method (ASTM C1074), the sensors calculate compressive strength automatically. This eliminates the need for physical samples or laboratory testing, streamlining the entire concrete testing process.
One notable example is the SmartRock™ Wireless Concrete Sensor. This sensor attaches directly to rebar and collects temperature data continuously. It then calculates the concrete’s strength and updates the results every 15 minutes. You can access this information remotely through the SmartRock™ mobile app or the Giatec 360™ dashboard. This level of accessibility ensures you stay updated on your project’s progress, even when you’re off-site.
The benefits of wireless maturity sensors extend beyond convenience. They enhance accuracy by providing consistent and reliable data. You can identify potential issues early, such as improper curing conditions, and take corrective actions immediately. Additionally, these sensors reduce costs by eliminating the need for frequent lab tests and minimizing delays caused by waiting for results.
For instance, if a project requires a specific compressive strength before removing formwork, wireless maturity sensors allow you to verify this in real-time. This prevents premature removal, which could compromise structural integrity.
By incorporating wireless maturity sensors into your construction workflow, you improve efficiency, reduce risks, and ensure the quality of your concrete. These tools represent a significant advancement in concrete testing, making them an essential asset for modern construction projects.
Importance of Concrete Testing in Construction
Concrete testing plays a pivotal role in ensuring the success of construction projects. By evaluating the material’s properties, you can confirm its suitability for your structure and prevent costly failures. Below are the key reasons why concrete testing is indispensable in construction.
Ensuring Structural Safety
Structural safety is the foundation of any construction project. Concrete testing ensures that the material can withstand the loads and stresses it will encounter. Without proper testing, undetected weaknesses in the concrete could lead to catastrophic failures.
Statistics reveal that approximately 15% of construction failures stem from issues related to cement quality. This highlights the critical need for rigorous testing throughout the construction process. By conducting quality tests, such as compressive strength and tensile strength evaluations, you can identify potential problems early and address them before they compromise the structure.
“Regular cement testing creates stronger, safer structures,” according to industry best practices. These tests ensure that the concrete meets design specifications, providing peace of mind that your project will stand the test of time.
Meeting Regulatory Standards
Compliance with regulatory standards is non-negotiable in construction. Authorities enforce strict guidelines to ensure public safety and environmental sustainability. Concrete testing helps you meet these requirements by verifying that the material adheres to established benchmarks.
For example, compressive strength tests confirm that the concrete can bear the required loads, while permeability tests ensure resistance to environmental factors like water and chloride ions. By adhering to these standards, you not only avoid legal penalties but also enhance the credibility of your project.
Testing also demonstrates your commitment to quality and safety, which can strengthen your reputation in the industry. Meeting regulatory standards through proper testing reflects professionalism and builds trust with stakeholders.
Enhancing Durability and Longevity
Durability and longevity are essential for any structure. Concrete testing allows you to assess the material’s ability to resist wear, environmental stress, and chemical reactions over time. By understanding these properties, you can make informed decisions to improve the concrete’s performance.
Tests like the drying shrinkage test and chloride ion penetration test help you identify vulnerabilities that could lead to cracking or corrosion. Addressing these issues during the design phase ensures that your structure remains robust and functional for decades.
For instance, optimizing the water-cement ratio based on test results can significantly enhance the concrete’s durability. This proactive approach reduces maintenance costs and extends the lifespan of your project.
The importance of concrete testing cannot be overstated. It safeguards structural safety, ensures compliance with regulations, and enhances the durability of your construction. By incorporating various types of concrete tests into your workflow, you can deliver projects that are not only safe but also built to last.
Reducing Costs by Preventing Failures
Concrete testing plays a crucial role in saving costs by identifying potential issues before they escalate into expensive failures. When you conduct thorough tests during the construction process, you ensure that the concrete meets the required standards for strength, durability, and performance. This proactive approach minimizes the risk of structural defects, which can lead to costly repairs or even complete reconstruction.
Failures in concrete structures often result from undetected weaknesses, such as improper mix proportions, inadequate curing, or environmental exposure. By performing regular tests, you can detect these problems early and take corrective actions. For example, a compressive strength test can reveal if the concrete can bear the intended load. If the results fall below the required threshold, you can adjust the mix design or curing process immediately, avoiding future complications.
“Regular cement testing throughout concrete manufacturing and implementation consistently creates stronger, safer structures that perform well under varying conditions.” This principle highlights how consistent testing not only ensures safety but also prevents financial losses caused by structural failures.
Preventing failures also reduces indirect costs, such as project delays and legal liabilities. A failed structure can halt construction, leading to extended timelines and increased labor expenses. Additionally, addressing failures after construction often involves legal disputes, further inflating costs. By investing in concrete testing upfront, you safeguard your project against these risks and maintain its financial viability.
Incorporating advanced testing methods, such as wireless maturity sensors, can further enhance cost efficiency. These tools provide real-time data on concrete strength, allowing you to make informed decisions without waiting for lab results. This reduces downtime and ensures that your project progresses smoothly.
Concrete testing is not just a quality control measure; it is a cost-saving strategy. By preventing failures, you protect your investment, avoid unnecessary expenses, and deliver a structure that stands the test of time.
Concrete testing is essential for ensuring the success of your construction projects. By understanding the various types of concrete tests, you can select the most suitable methods to evaluate the material’s properties. Quality tests help you verify the strength, durability, and safety of concrete, reducing the risk of structural failures. These tests also ensure compliance with industry standards, saving time and costs in the long run. Rigorous quality tests not only enhance the performance of your structure but also contribute to its longevity. Prioritizing these evaluations safeguards your project and builds trust in its reliability.