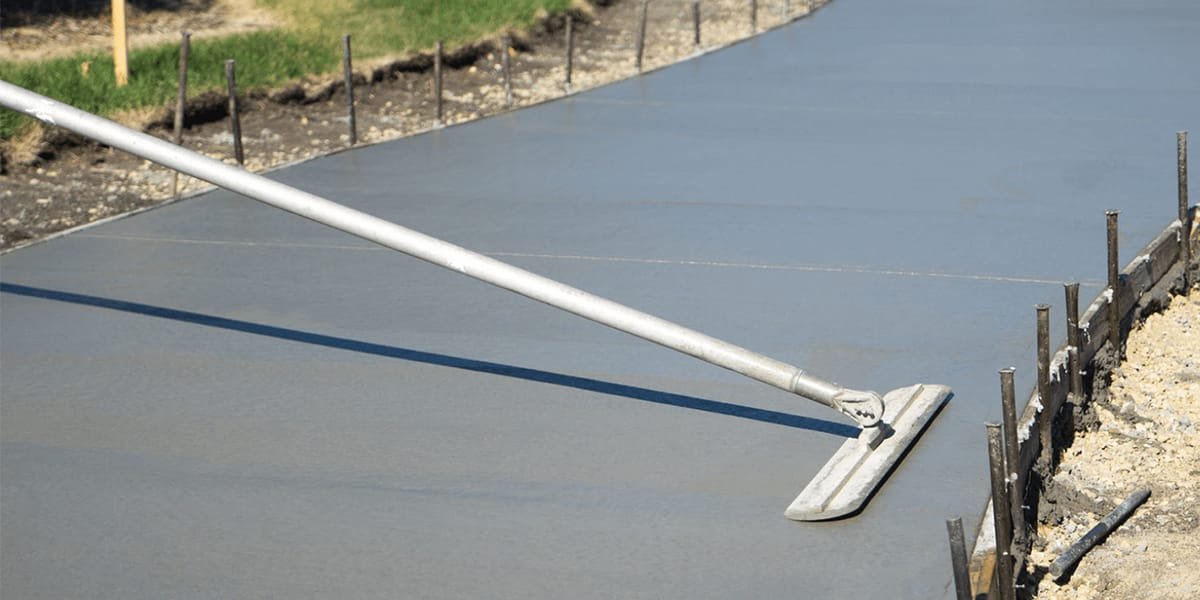
05 Mar What Is a Concrete Road?
Concrete roads offer long-term performance and cost savings. But what sets them apart from asphalt roads? Are concrete roads better than any other type of road? Let’s take a deep dive into this article to find your answers!
A concrete roadway is made from cement, sand, coarse aggregate, and water. It is strong, durable, and requires little maintenance. Concrete is an ideal material for highways and heavy-load areas.
This guide will explain the construction and functionality of concrete roads.
What Is a Concrete Road?
A concrete road has concrete as its main material. Let us look at the composition of concrete roads in detail.
Composition
The main components used in concrete roads are:
- Cement.
- Sand.
- Coarse Aggregate.
- Water.
These components are carefully proportioned and mixed to achieve high compressive strength and durability.
Design
Concrete roads are made using two methods: concrete slabs and concrete pouring. Concrete slabs are laid with expansion joints, which allow the concrete to expand in summer and contract in winter.
In continuous concrete pouring, concrete is poured directly into the formwork. And later leveled using flat tools. Expansion joints are also placed in the continuous concrete pouring method.
Purpose
Concrete roads last for a long time. They can also bear heavy traffic without cracking or breaking.
How Are Concrete Roads Constructed?
Concrete roads are carefully constructed. Let’s break down the construction process using the continuous concrete pouring method.
- Preparation
The first step is preparing the site. The site is cleaned, and any bumps or depressions are removed. After cleaning the site, a sub-base of gravel or crushed stone is placed on the site. This sub-base is compact and acts as a structural support of concrete roads.
- Formwork and Reinforcement
Wood or steel formwork is placed on the edges of the road to ensure width, shape, and length. For reinforcement steel is placed inside the fromwork to improve the tension strength of concrete.
- Concrete Pouring and Finishing
Concrete ingredients are thoroughly mixed and poured inside the mold. After pouring, flat tools are used to even out the concrete. Finishing provides a smooth and leveled concrete surface.
- Curing and Joints
Engineers decide when to place an expansion joint. For example every 4 feet. So engineers will place a joint former at every 4 feet on wet concrete. These joint formers create a gap to allow expansion and contraction according to weather.
Concrete roads are properly cured to ensure high compressive strength. An adequate amount of moisture is provided during the curing process. Also, no load is added to the rod during curing.
Advantages of Concrete Roads
Concrete roads offer many benefits. They can bear heavy loads without cracking or breaking. Let’s discuss all the advantages in detail.
Durability
Concrete roads have a longer lifespan because of high compressive strength. Concrete roads last, on average, 30 years. Asphalt roads last 18 years.
Low Maintenance
Concrete roads have a high cement ratio and reinforcement. These two elements give concrete roads strength. They protect against wear, making concrete roads low maintenance.
Strength
Concrete roads are strong. They can bear heavy traffic and heavy lloadsStrenght is one of the main reasons, concrete roads are chosen over asphalt roads.
Environmental Benefits
Concrete roads are eco-friendly. They reduce fuel use by helping heavy vehicles save up to 0.45 liters of fuel per 100 km. They reflect sunlight, reducing the heat island effect. They also reabsorb 21% of the carbon dioxide released during cement production.
Economical in the Long Term
Concrete roads are economical in the long term. They last a long time and need little maintenance. For example, a concrete road can last up to 30 years. That means no road work is needed for three decades.
Disadvantages of Concrete Roads
There are some disadvantages attached to concrete roads. Let us discuss them in detail.
High Initial Cost
High-quality cement, sand, and coarse aggregate are required for concrete roads. These high-quality materials are expensive. Also, the construction work of concrete roads requires site preparation and machinery. All of this creates a high initial cost of concrete roads.
Longer Construction Time
Concrete requires curing to reach its full strength. The curing time ranges from 7 to 28 days. Curing time delays road access to any load or vehicle. The construction process of concrete roads is also time-consuming.
Less Flexibility
Concrete roads are less flexible than concrete roads. If they are not carefully constructed or cured. This can result in cracks or worse the breaking of concrete roads. Sometimes the subbase can also move or shift, disrupting the structural integrity.
Noise
The rough surface of concrete roads can generate noise upon vehicle moment. This disadvantage can be mitigated with textured or grooved surfaces.
Where Are Concrete Roads Used
Concrete roads are used for the following:
Highways
Concrete roads are a perfect choice for highways. Highways face heavy traffic loads, making concrete roads an ideal option. Concrete roads are strong and durable and can withstand the heavy traffic of highways.
Urban Roads
Urban roads not only have heavy traffic loads but also face harsh weather. The durability of concrete roads makes them a perfect fit for urban roads. Concrete roads also add to the overall aesthetic of urban areas.
Industrial Zones
Industrial zones face heavy machinery, heavy truckloads, and load/unloading. Concrete roads because of their strength can withstand frequent movement of machinery and trucks.
Bridges and Overpasses
Concrete is a strong and durable material. Due to its compressive strength, it can withstand pressure without cracking or breaking. And bridges and overpasses need to be strong and secure. This makes concrete an ideal material for bridges and overpasses.
Maintenance of Concrete Roads
The following tips can increase the lifespan and overall condition of concrete roads.
- Regular Inspections
Regularly inspect concrete roads for early detection of any fault. Check for cracks, depressions, and noise pollution. Regular inspections help solve small problems in time. Regular inspection also prevents bigger problems and keeps concrete roads working for a longer time.
- Sealing Joints
Expansion joints should be sealed carefully to prevent water infiltration and chemicals. Sealing joints of concrete roads also maintain the structural integrity of concrete by protecting the sub-base.
- Repairs
Do not ignore minor damages to concrete roads. Repair cracks or any other error promptly. This prevents bigger problems and increases the overall life span of concrete roads.
Conclusion
The composition of concrete roads makes them strong and durable. Concrete roads can be prepared using two methods. Concrete roads have a longer lifespan than asphalt roads.
There are many benefits of concrete roads, including low maintenance. Concrete roads also have disadvantages, like longer curing time.
Overall concrete roads are the best option for highways, industrial zones, bridges, etc.