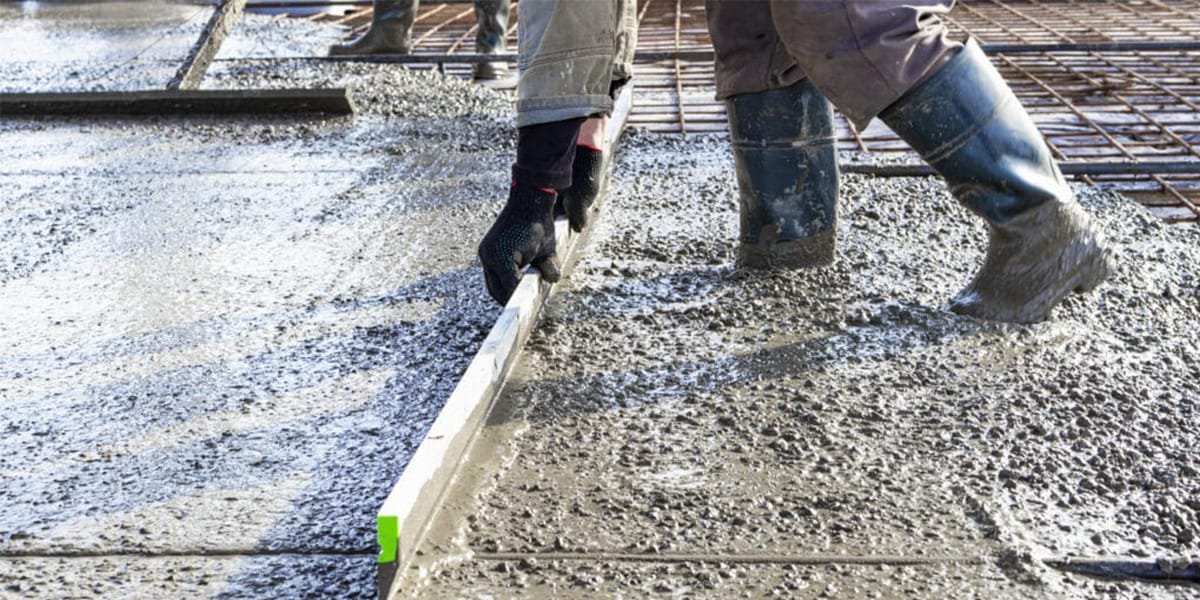
14 Dec What Is High Performance Concrete Used For?
High-Performance Concrete (HPC) has revolutionized civil engineering. It is the number-one demand of many projects today due to its superior properties than traditional concrete. In this article, we will discuss what HPC is, where you should use it, and how.
HPC is widely used for structures that are meant to suffer extreme load, pressure, weather, and many dangerous conditions.
Keep reading to learn about what these applications are and why HPC is the best choice for such projects.
What Is High-Performance Concrete?
HPC overcomes the limitations of conventional concrete. It provides more strength, resistance, and durability.
Higher Compressive Strength:
HPC achieves the compressive strength of 10,000 psi within 28 days. Normal one may only get 5,000 psi in the same amount of time. HPC’s greater performance stems from its composition. It contains Portland Cement, good quality aggregates, active silica, and superplasticizers.
Increased Durability:
Structures made with HPC can withstand extreme weather, heavy wear, and chemical exposure. Unlike conventional concrete, it doesn’t get capillary pores from the hydration reaction. These pores absorb water and adversely impact the material’s durability.
This concrete maintains 80% of its strength even when frozen and thawed repeatedly over 300 times. The building can last longer and require less maintenance if it’s made with HPC.
Reduced Permeability:
HPC has a low permeability, meaning it limits water (H2O) and chloride (Cl) from penetrating in. H2O and Cl can corrode the reinforcement bars (rebars) inside the concrete structure.
Applications of High-Performance Concrete
HPC is widely used in various sectors. Here are some of the examples:
Bridges and Overpasses:
Bridges and overpasses endure heavy traffic and extreme weather very often. HPC can protect these infrastructures from frequent repairs. You can build them with even less support using HPC, and it won’t affect their durability.
Furthermore, it also resists de-icing chemicals that are spread on roads and bridges to melt ice. These chemicals can seep into regular concrete, corroding the rebars and weakening the structure over time.
High-Rise Buildings:
High-rise buildings have a massive vertical load. It includes the weight of building materials, equipment, people, and water and snow accumulation on the roof. HPC reduces the impact of these forces and allows builders to make even taller skyscrapers.
Marine Structures:
The integrity of marine structures like piers, jetties, and offshore rigs is constantly under threat. High water pressure and strong waves cause cracks, abrasion, and potential collapse. HPC enables them to survive saltwater corrosion so they can last long underwater.
Industrial Floors:
Industrial floors see severe traffic of different vehicles, equipment, and machinery every day. A regular floor deteriorates quite often, increasing the cost of maintenance. HPC saves time and money by bearing all the harshness without rupturing.
Moreover, its dense microstructure due to active silica allows it to resist almost all chemicals. In factory or warehouse settings, chemical spills are a common occurrence.
Nuclear Power Plants:
HPC can handle all the intense pressures and temperatures that nuclear reactors generate. It blocks the radiation from escaping and harming humans and the environment.
Benefits of High-Performance Concrete in These Applications
These applications can enjoy the following advantages thanks to HPC:
Longevity:
A key benefit of using HPC in any project is longevity. This powerful concrete is susceptible to damage. You need fewer repairs, which means more cost-saving. Structures made with HPC can last a century longer than those made with traditional concrete.
Sustainability:
The higher strength and durability of HPC make it a sustainable choice in modern construction. You use less material for the same capacity that would require a larger quantity of traditional concrete. You can also reduce energy consumption and waste by using less amount of concrete.
Improved Safety:
HPC guarantees the safety of the structure and those inside it. As it shields against damages and degradation, there is almost no chance of accidental collapse.
Aesthetic Flexibility:
If you want to build an architectural masterpiece, HPC is the best option. It can help you make any design that is not possible with traditional concrete. You can create sleek shapes, sharp edges, and delicate curves on thin areas while maintaining the same level of durability.
Conventional concrete cannot do that because it requires a thicker area to work on. As a result, the structure gets the same typical outlook with no sign of innovation.
Limitations to Consider When Using High-Performance Concrete
Despite its many benefits, HPC has some limitations that you need to consider before using it.
Cost:
The main drawback of HPC is its cost. It is way more expensive than normal concrete due to premium materials. It may contain a higher grade of Portland Cement, which increases cost. The special aggregates and plasticizers used in HPC are also costlier than regular ones.
Specialized Handling:
HPC also requires expert handling. You need highly skilled labor to mix the correct proportions of the ingredients. A minor mistake can severely compromise the mixture. If HPC doesn’t get all of its properties, it will not provide the desired strength and durability.
Curing Requirements:
The curing part is also challenging when it comes to HPC. It needs more time to cure compared to traditional concrete. This means there’s more risk of moisture getting trapped if you don’t manage properly.
Builders often use curing membranes to assist with the process. However, this addition evidently increases the overall cost.
How to Ensure Successful Use of High Performance Concrete
Here are some guidelines to ensure the successful use of HPC in any application:
1. Choose the Right Mix Design:
Different structures have different needs. Choose the right materials and adjust their proportions according to the structure’s demands. For example, if you want to use HPC on marine structures, you need to increase the quantity of active silica.
2. Work with Experts:
Work with skilled professionals to prepare the mixture and pour it into forms. They must be familiar with these high-performance additives to create a proportional mix. Placing the HPC also requires a proper procedure. An expert ensures that the pour sets evenly without creating air pockets.
3. Monitor Curing Conditions:
Keep monitoring the temperature and moisture levels as HPC cures. The moderate temperature is usually between 10 to 21 degrees Celsius. It is enough to prevent the concrete from drying or freezing.
You also have to keep the structure moist for 7-28 after applying HPC. You can do that by watering it or using curing sprays.
4. Plan for Testing:
Conduct tests to verify whether the HPC has met the intended specifications. Testing can allow you to identify potential issues that can compromise the final material.
Conclusion
Many applications today necessitate the use of HPC. Despite the high cost, it is widely used to enhance the durability of critical urban infrastructure. Consider it as a long-term investment rather than a cost. It will surely have more applications in the future.