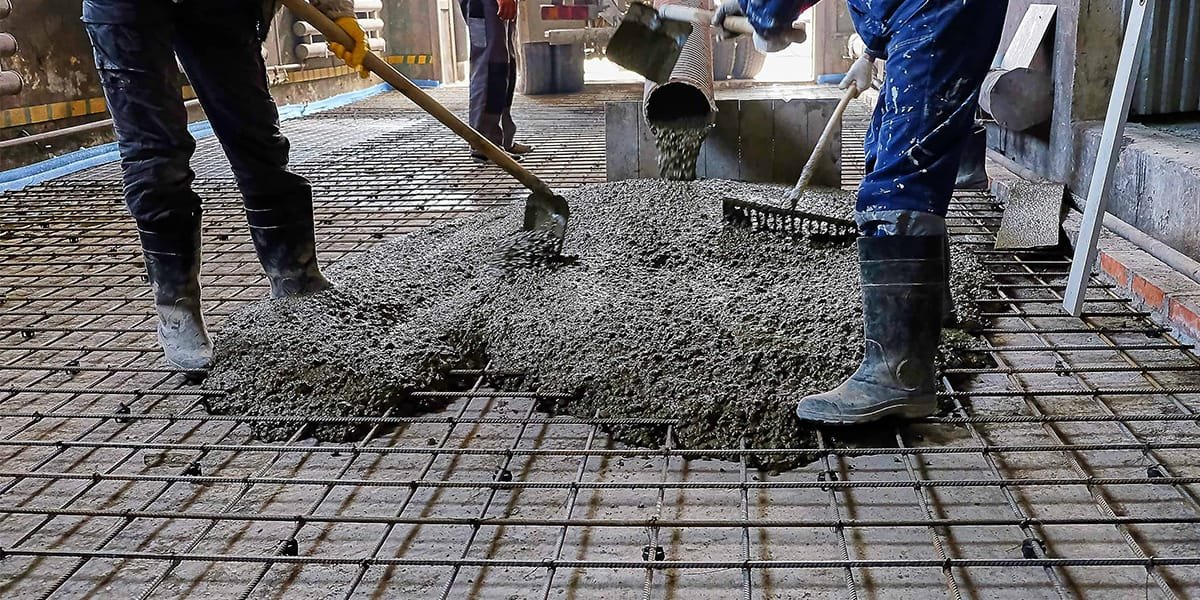
07 Mar What Is The Different Types Of Concrete Grades And Their Uses?
The durability of your construction depends on the strength of the concrete you use. And that strength comes from the concrete grade. This article provides valuable insights into different concrete grades and their uses.
Concrete grades specify how strong the mix becomes within 28 days of curing. The unit that measures the grade is megapascal (MPa), where “M” means mix, and the number indicates its compressive strength.
Read on to learn about concrete grades, their types, applications, and factors that affect their strength.
What Are Concrete Grades?
Have you ever seen a letter and number like “M20” on a bag of concrete mix? That is its grade. It means that the respective concrete will achieve 20 Mpa at the 28-day mark. This is an expected period for concrete to reach its optimum but not full strength.
The concrete mix continues to strengthen even after 28 days of pouring. Different concrete grades have different proportions of ingredients. For example, M20 normally has a ratio of 1:1.5:3. It means the mix contains 1 part cement, 1.5 parts fine aggregates, and 3 parts coarse aggregates.
Types of Concrete Grades and Their Uses
There is high-grade concrete and low-grade concrete, each with its own uses. As the grade gets low to high, the value of Mpa increases in multiples of 5.
Low-Grade Concrete (M5 to M15):
Low-grade concrete usually starts from M5, which has a compressive strength of 5 Mpa. Grades M10 and M15 are also categorized as low-grade concrete. They have compressive strengths of 10 and 15 Mpa, respectively. The mix ratio for each is: M5 = 1:5:10, M10 = 1:3:6, and M15 = 1:2:4.
This level of strength is only suitable for non-structural applications. Builders normally use lower grades for constructing flat surfaces that do not bear heavy loads. For example, you can build pathways and curbs with M5, M10, and M15 grades.
Standard-Grade Concrete (M20 to M25):
After M15 come M20 and M25, which are standard grades at 20 and 25 MPa, respectively. As M20’s mix ratio is mentioned above, M25’s is slightly different at 1:1:2. It contains more cement and less aggregates for enhanced strength at the expense of workability.
Both types are Reinforced Cement Concrete (RCC), which is the backbone of today’s urban construction. You can use it in projects that will sustain moderate to heavy loads. Most prefer the M20 for building houses due to its perfect balance of strength and workability.
High-Grade Concrete (M30 to M50):
For projects requiring more strength than 25MPa, high-grade concrete is the ideal choice. Its grades range from M30 to M50, offering more load-bearing capacity and weather resistance with each grade. It is often called high-performance concrete (HPC). Its compressive strength ranges from 30MPa to 50MPa.
Projects that require high-grade concrete withstand significant pressures. Roads, highways, infrastructures, skyscrapers, bridges, and underwater constructions all need at least M30.
Ultra-High-Grade Concrete (Above M50):
All grades beyond M50 are Ultra High-Performance Concrete (UHPC). The highest possible strength they can reach is around 236 MPa. Anything above that is Reactive Powder Concrete (RPC), which goes up to 810 MPa. RPC is different from conventional concrete as it includes steel fibers as aggregates instead of gravel.
RPC is highly overpowered; most construction may not even require an MPa greater than 200. Concrete grades ranging from M50 to M60 are enough for containing nuclear energy inside power plants. Moreover, you can use them to create industrial floorings that resist wear and tear for longer periods.
How to Choose the Right Concrete Grade
The previous section highlighted the types of concrete grades. Now, it is time for understanding how to choose the right one for the job at hand.
Determine the Purpose:
The first step in this decision-making process is defining the purpose of the concrete grade. Does your project require structural or non-structural concrete? The material used for structural purposes is higher in strength and cost. Therefore, if you just want to construct a walkway outside your house, M10 is sufficient.
Consider Load Requirements:
Walkways and patios do not have to bear heavy loads. M10 or M15 can perfectly handle the weight of people walking on these constructions. However, if your project involves building a driveway, then you will need at least an M20 grade. Similarly, adding another storey to the house may require an even higher grade.
Assess Environmental Conditions:
You may also have to use multiple grades of concrete on the same project you are working on. Different parts of the structure can be exposed to various external conditions.
Some walls only see moderate rain and sun, so M20 can be sufficient for them. However, others can be vulnerable to snow. If the M20 can take around 100 free-thaw cycles (FTC), the M35 can endure 250.
Similarly, in an industrial setting, you have to take into account the areas with chemical exposure. Higher grades, M30 and above, are denser, so they resist damage from chemicals better than low-grade ones.
Follow Building Codes:
Besides personal preferences, you have to consider local standards and guidelines for recommendations. Various standards specify the mix design for each grade so it can perform as expected. They also clearly highlight the applications where they should be used. For example, China’s GB 50010 recommends 30MPa of compressive strength for roads with moderate to heavy traffic.
Factors That Affect the Strength of Concrete Grades
The final section of the article clarifies how each grade of concrete differs in strength.
Mix Ratio:
The key factor that affects the strength of concrete grades is the mix ratio. Adjusting the proportions of cement and aggregates dictates whether your concrete is high or low grade. Higher grades of concrete have more cement and less aggregates, and vice versa. For example, if you add more sand to the M30 mix, it will likely become closer to M25.
Curing Conditions:
The second-most important factor in strengthening the concrete grade is curing. After placing the concrete, keep it moist for 28 days. This allows the hydration to continue uninterrupted for the concrete grade to reach its expected strength.
Quality of Materials:
The quality of the materials used to make the concrete grade also significantly impacts its final strength. Each ingredient, i.e., cement, aggregates, and even water, should be of good quality.
You can check the quality of cement in a lot of ways. One method is to perform a float test. It involves sprinkling a small amount of cement in a bucket of water. If it floats for a while, it is fine, but if it sinks immediately, it’s compromised.
Similarly, jagged rocks are better aggregates than smooth ones. They can interlock easily when concrete is placed on the structure, preventing it from deforming under load.
Water can also contain impurities, which can hinder the hydration reaction and reduce concrete’s strength. That is why the American Concrete Institute (ACI) recommends using drinking water to make concrete.
Admixtures:
The concrete grade, on its own, may not be specific enough for your project. You have to add some admixtures to modify its properties. These are chemical compounds used to improve the strength, durability, set time, and workability of the concrete.
Many types of admixtures serve different purposes. Most high-grade concrete mixtures have superplasticizers. When you add water to the mix, the cement particles start to clump together and trap some of the liquid. Superplasticizers disperse those particles, freeing the water and allowing more workability.
Conclusion
In the end, it is essential to note that the strength of concrete does not solely depend on its grade. It is the interplay between all the aspects mentioned in this article. Every stage of the process is as important as choosing the right grade.