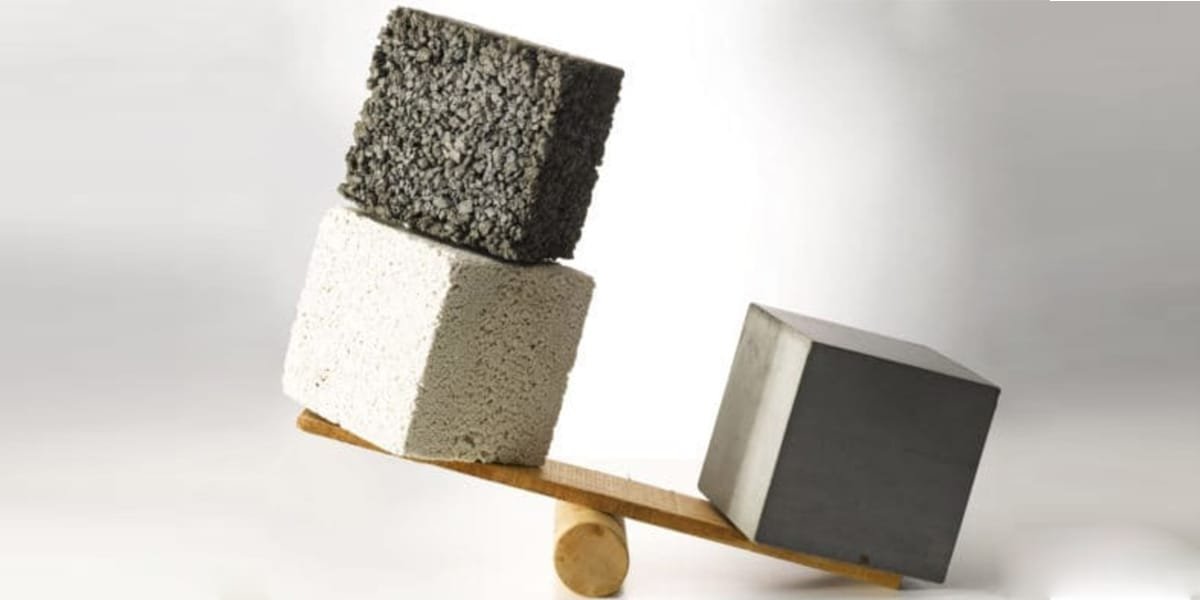
13 Feb What Is The Lightweight Concrete?
Lightweight concrete (LWC) weighs less than regular concrete for a solid reason. This article explains the material in detail and provides best practices for its applications.
LWC is made of lighter coarse aggregates than the ones used in traditional concrete. These lightweight ingredients include expanded clay, shale, and polystyrene beads. They significantly reduce the concrete’s weight and improve thermal insulation.
Here’s everything you need to know about LWC, its limitations, applications, and tips for using it effectively.
What Is Lightweight Concrete?
LWC is a type of concrete that has a lower density, ranging from 400 to 1,800 kg/m³. This is 25-30% lighter than the standard concrete, which is normally between 2,200 to 2,400 kg/m³. This reduced weight is due to lightweight aggregates and specific chemicals.
It also has a higher water content because light aggregates absorb a lot of moisture. This huge amount of water compromises durability and strength, so it’s for structures that do not bear heavy loads.
Types of Lightweight Concrete
LWC comes in many different types. Here’s how each type is created to cover various aspects of construction:
Lightweight Aggregate Concrete:
The main type of LWC is lightweight aggregate concrete (LWAC). Instead of gravel or crushed rocks, LWAC contains expanded clay, shale, ash, perlite, slate, or volcanic pumice. These light materials are heated in klin to make them porous. Then, they are soaked in water before being added to the mix.
LWAC is used to construct structures with less mass but sufficient strength and durability. Concrete blocks and cylinders used to make houses are often made with LWAC.
Aerated or Foamed Concrete:
The second most common type of LWC is Aerated or Foamed Concrete. It is made by intentionally creating voids in the concrete mix, a practice known as air entrainment. Tiny air bubbles are released into the mix using chemical admixtures called air-entraining agents.
This type of concrete is ideal for increasing thermal insulation in construction. It can be used in non-load-bearing walls while constructing energy-efficient buildings. Porous structures trap air within and maintain stable temperatures indoors for longer periods.
No-Fines Concrete:
Another type of LWC is No-Fines concrete or pervious concrete. It only contains coarse aggregates and no fine sand. This composition focuses on draining water through larger voids. Fine sand, a key component of standard concrete, creates smaller pores that stop water from moving.
These properties make No-Fines concrete suitable for projects where water drainage is a major concern. Soil can only absorb too much rainwater or snowmelt. This is why No-Fines concrete is used in drainage systems or permeable pavements to guide water to the ground below.
Benefits of Lightweight Concrete
The light weight of LWC doesn’t mean it is weak for construction. In fact, there are several benefits to using it in specific projects.
Reduced Weight:
The main advantage of LWC is that it’s easier to handle and transport. Most precast construction elements are made of LWC to facilitate this convenience. It not only reduces labor and logistics costs but also speeds up overall construction.
Improved Insulation:
Many sustainable homes and classrooms use LWC because of the improved thermal and sound insulation. Its thermal insulation is about ten times superior to standard concrete. The lower density also improves soundproofing in concrete, leading it to absorb echos and vibrations.
Eco-Friendly:
LWC is more eco-friendly than its counterpart because it consumes less natural resources. This way, its production has a lower impact on the environment. Even its aggregates are recycled materials, which would contribute to waste if not for LWC.
Reduced Foundation Load:
The key advantage of using LWC is that your construction will have fewer dead loads. A lighter building places less stress on the foundation, so it can easily handle different structural demands.
Fire Resistance: Excellent fireproofing properties.
Several studies have concluded that LWC can be used as an official substitute for non-load-bearing walls. Its lower thermal conductivity boosts the fire resistance of your buildings. Whether it’s heat or fire, it spreads slowly across the structure.
Applications of Lightweight Concrete
Many applications benefit from the qualities of LWC. Here are some industries where it’s normally used:
Residential Construction:
Several elements in houses, complexes, and sheds are made with LWC. It is used to create insulation layers, non-load-bearing walls, and different decorative elements. Several roofs and floors can also be made with LWC to reduce dead load.
Commercial and Industrial:
LWC has also become popular in the commercial and industrial sectors. It has been used to create many precast panels and partition walls. Many hotels, malls, and corporate offices rely on its attested fireproofing.
Infrastructure:
LWC reduces the weight of infrastructure so they can keep on carrying the urban world. It removes significant weight from the bridge decks, allowing them to span longer without support. The pavements around the city also contain LWC, which is why they can stay cool under heat.
Marine Structures:
Because of its low density, LWC is also useful in some marine structures. Its very first use was in the marine industry as well when it was used to build ships. Today, it still serves the same purpose by creating lighter boat hulls for increased mobility. LWC’s buoyancy also supports various modern floating platforms.
Limitations of Lightweight Concrete
While it has so many benefits, it is also important to consider the potential shortcomings of LWC.
Lower Strength:
LWC is meant for structures that do not require heavy load-bearing capabilities. It has a lower compressive strength than the original concrete. After 28 days of curing, it reaches at least 17 MPa, with some formulations going up to 40 MPa. In contrast, the standard grades of concrete achieve 25 to 45 MPa compressive strength in the same period.
Higher Cost:
Producing lightweight aggregates like expanded clay, shale, and slate is a costly process. This is why LWC is more expensive than regular concrete, which uses natural aggregates like gravel and crushed stone. Some natural lightweight aggregates like pumice, scoria, and tuff also exist. However, they are rare in some regions, which increases transportation costs.
Workability:
Due to porous aggregates, LWC doesn’t offer much workability. These aggregates absorb too much water, which is why LWC needs a higher volume. Sometimes, it results in excess water, which causes segregation of ingredients in the mix. They float to the top of cement paste, reducing the concrete’s uniformity and strength.
How to Use Lightweight Concrete Effectively
To avoid potential mishaps that can render LWC useless, here are some tips to use it effectively.
- Choose the Right Type:
The first step is to choose the right type of LWC that meets your project’s needs. Different construction projects have individual structural demands. If you are working on a residential building, LWAC can be helpful in making it more energy-efficient. On the other hand, you can pick Aerated or Foamed LWC for pavements to drain rainwater easily.
- Control the Mix:
Next, choose the proportions of aggregates, cement, and water according to your project. Each application has separate requirements, so they need tailored mix designs. For example, if you want to reduce dead loads in walls and floors, use LWAC. Adjust the cement, water, and light aggregates ratio, which usually starts from 1:2:3.
- Use Admixtures:
Workability and strength are two main areas where LWC lacks. You can enhance them with specific chemical or mineral admixtures. For example, plasticizers can increase workability without adding more water. Similarly, you can use silica fume to enhance strength, as it fills the voids created inside LWC.
- Cure Properly:
Finally, make sure to follow proper curing protocols with LWC. It can lose a lot of moisture quickly, resulting in weaker construction. A recommended method is to cover the LWC with wet burlap blankets to retain moisture. There are also many curing compounds you can apply frequently to prevent LWC from drying.
Conclusion
LWC is rapidly gaining popularity in modern construction, where sustainability matters the most. It reduces dead weight, boosts insulation, and increases the building’s energy efficiency. Follow the tips above to maximize its benefits to your projects.